As noted earlier in the design section when discussing handling qualities, the horizontal stabilizer was sized using criteria involving a dimensionless coefficient known as the horizontal tail volume coefficient. Based on known good handling qualities of other sailplanes and the value of their tail volume coefficients, one can size the horizontal tail for Concordia. With the low wing area of Concordia and long tail boom of the fuselage, it turned out that the horizontal tail of the ASG29 would be good for Concordia if one limits the ship to aero tows only–no winch launches. Uli and Peter Kremer of Schleicher were generous enough to allow us use of the ASG29 horizontal tail mold for the Concordia tail if it could be done on a non-interference basis with ASG29 production. The original plan was to build the horizontal stabilizer while we were at Schleicher building the wing spar flanges but the mold was fully devoted to production during that time. Gerhard was able to make a trip back to Schleicher a few weeks later and build the horizontal stabilizer with a lot of help from others including Karl Klossok, Michael Greiner, Mario Link, Joachim Feige, and AS-specialist Harald Herget. The lamination scheme for the tail was different from the ASG29 since the required loads were greater, and again balsa was used as the core material. The stabilizer is mostly Kevlar with some carbon in high stress areas. The weight of the stabilizer using Kevlar and balsa was near that of the ASG29 even though it was built to carry additional loads. Don’t ask about the man-hours to build the stabilizer versus that of the ASG29; you can guess the answer to that question–many more hours.
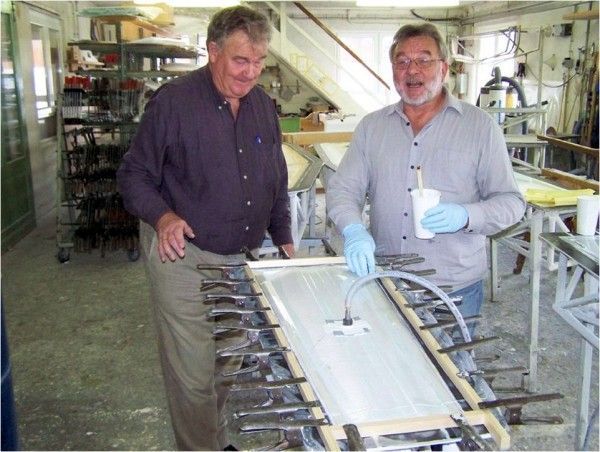
Gerhard and Karl Klossok applying a vacuum to one of the horizontal stabilizer skin laminations (click to enlarge)
5 comments for “Building Concordia-The Horizontal Stabilizer”